Why is spray foam insulation such a headache when buying a house?
2/12/20253 min read
Spray foam insulation gained popularity in the UK due to its ability to provide high-performance thermal efficiency, particularly in hard-to-reach areas like lofts. By expanding on contact, spray foam fills gaps and cracks, creating a seamless barrier that helps keep homes warm. However, while it seems like a quick fix for energy efficiency, spray foam insulation comes with some serious drawbacks—particularly when it’s used in lofts.
One of the primary concerns with spray foam in lofts is its impact on building ventilation. Proper ventilation is crucial in preventing moisture buildup, and spray foam can trap moisture inside the loft space. This trapped moisture can lead to the growth of mould and rot, which damages the structure of the house and poses health risks to the occupants. Additionally, spray foam can interfere with the natural movement of air through a building, leading to longer-term issues with dampness and indoor air quality.
Another issue is that spray foam can complicate future repairs or renovations. If you need to replace pipes, wiring, or even remove the foam for other reasons, it can be costly and challenging to remove the spray foam without causing damage to your home. This lack of flexibility is a key reason why mortgage lenders are hesitant to approve loans for homes with spray foam insulation.
Mortgage lenders are increasingly reluctant to lend on properties with spray foam in the loft due to concerns about its long-term effects on the property. The risk of hidden damage, such as mould, structural degradation, and the potential difficulty of conducting future repairs, makes these properties less appealing to buyers and harder to value accurately.
Spray foam insulation can be flammable. When it is initially applied, the foam itself is typically fire-resistant to some extent due to the chemicals used in its formulation. However, once the foam has fully cured, it can catch fire if exposed to a significant heat source or flame. The foam is made from polyurethane or similar materials, which are inherently combustible under certain conditions.
There are two broad types of spray foam insulation; open-cell and closed-cell. The differences lie in their structure, which impacts their performance, cost, and suitability for different applications. Here's a breakdown of the two:
Open-Cell Spray Foam
Structure: In open-cell foam, the cells (tiny bubbles) are not fully enclosed, meaning air can fill the gaps between them. This makes the foam more flexible and softer.
R-Value: Open-cell foam typically has a lower R-value per inch (around 3.5 to 4.0), meaning it offers less thermal resistance than closed-cell foam.
Water Resistance: Open-cell foam is not water-resistant. It can absorb water and may retain moisture, which could lead to mold or mildew problems in certain conditions.
Sound Insulation: Open-cell foam is great for soundproofing because of its ability to absorb sound waves.
Cost: Open-cell spray foam tends to be less expensive than closed-cell foam, making it a more affordable option for large areas like walls or ceilings.
Applications: It is often used in interior applications, such as walls and attics, where moisture is less of a concern, and soundproofing is desired.
Closed-Cell Spray Foam
Structure: In closed-cell foam, the cells are completely sealed, which gives it a denser, more rigid structure.
R-Value: Closed-cell foam has a higher R-value per inch (around 6 to 7), providing superior thermal insulation and efficiency.
Water Resistance: One of the key benefits of closed-cell foam is its water resistance. It does not absorb moisture, making it ideal for areas prone to water exposure, such as basements or exterior walls.
Sound Insulation: Closed-cell foam offers some soundproofing, but it is less effective than open-cell foam for this purpose.
Cost: Closed-cell foam is more expensive due to its superior performance and higher density.
Applications: It is often used in areas where moisture resistance is crucial, such as basements, crawl spaces, and exterior walls. It's also used in roofs or commercial buildings where additional strength and rigidity are needed.
Open-cell foam is softer, more affordable, provides good soundproofing, but has lower insulation performance and absorbs water.
Closed-cell foam is denser, more expensive, offers higher insulation, is water-resistant, and provides better structural integrity.
In conclusion, while spray foam insulation can offer excellent energy efficiency and reduced heating costs, UK housebuyers should carefully consider its potential pitfalls. The material can be difficult to remove or replace, leading to costly repairs if it becomes damaged or degrades over time. Additionally, improper installation may result in trapped moisture, which can contribute to mould growth and structural damage. Moreover, spray foam can interfere with the performance of other building systems, such as ventilation and wiring, if not installed correctly. Therefore, prospective buyers should ensure thorough inspections and weigh the long-term implications before committing to a property with spray foam insulation.
© 2025 ALS Consulting Ltd. All rights reserved.
Registered Company Number 15224395.
Tel: 07441 342 454
Email: adam@als-consulting.co.uk
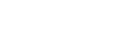
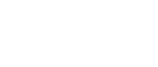
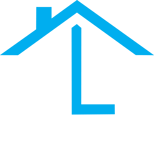
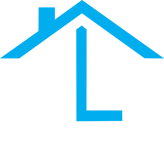
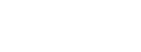
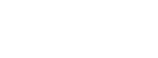
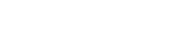
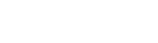
Privacy Policy